China’s Export Porcelain
Photos by Forrest Anderson
Fashion, technology, terminology, social and political values, ceremony, and biography could all be explored by examining something as simple as a teacup.
— Mark Howell
Europeans once called the delicate, finely painted Chinese porcelain bowls and cups that arrived at their ports “white gold.” A relatively minor commodity among the goods traded with China compared with tea, silk, spices, opium and silver, porcelain has since acquired an outsized value to historians because of its durability and decorative nature. Unlike other products, porcelain's history is branded onto its gleaming surface. It has survived, even in shipwrecks and on deserted beaches, to tell the story of hundreds of years of Chinese trade with the world. Porcelain enriches the study of history, art, culture, social customs, trade routes, political and economic trends and cross-cultural interaction.
The European love affair with Chinese porcelain, along with the voracious policies of imperial Europe and Qing Dynasty China, shattered the 1,500-year-old Chinese porcelain industry which was one of the world’s finest technological and artistic achievements. The tale of Chinese export porcelain traditionally was spun by Western sources as beginning with Vasco Da Gama’s voyage around the Cape and culminating in the Europeans’ discovery of the secret of porcelain which ended their dependence on the Chinese porcelain trade. However, the record is much different when European accounts are combined with Chinese, Mexican, and other sources.
Chinese legend credits the Yellow Emperor who founded the Chinese empire with appointing an official to manage pottery making. An immortal luckily passed by and helped the official control fire so he could build a kiln. One day, he entered it to observe the pottery firing and was burned to death. The archaeological record reveals that pottery appeared in the Neolithic era nearly 10,000 years ago, spurred by agricultural advances that created a need for vessels for cooking and storing food. Taken for granted today, the development of pottery, then stoneware and finally porcelain was a monumental task that required the collective ingenuity of thousands of potters over millennia. Fine quality Chinese pottery dates as far back as 7,900 years ago. Neolithic Chinese potters produced highly artistic pottery in a variety of styles, including fine Longshan ware as thin and smooth as an eggshell. They perfected use of the potters’ wheel, firing at high temperatures, and impressed designs. Potters were ranked first among Shang China’s artisans, so high that a Shang king gave his daughter’s hand and chiefdom of a vassal state to a skilled potter. A wide variety of ceramics and large workshops with a division of labor have been excavated from this period. Among the era’s fine wares was a pottery made of white kaolin clay fired at about 1,000 degrees Celsius. By 200 BC, Chinese potters had achieved superb skill as evidenced by the terracotta warrior army at Xi'an, China, which demonstrates sophisticated assembly line technology.
Porcelain uses a complicated mixture of kaolin, feldspar and quartz of porcelain stone to form a paste. It requires a coating of vitreous glaze which must be fired at a temperature of at least 1,250 degrees Celsius until needle-like crystals appear with vitreous particles filling the spaces between the crystals. This makes it non-porous and resonant when struck and gives it luster and smoothness. The process of achieving this quality required centuries of experimentation with combinations of clays, glazes, shapes and firing methods as well as finding places with a ready supply of raw materials, fuel for kilns and conditions for building certain kinds of kilns to produce the desired effects. Scholars differ on when true porcelain was achieved.
This Chinese export earthenware vessel from the 6th century is in the style of a West Asian pilgrim's flask, with a design similar to that of the culture of Sogdia. Merchants from Sogdia, in the area that is now Uzbekistan, were active along the Silk Road trade routes that stretched from China to the Middle East. The vessel is at the Metropolitan Museum of Art, New York.
The development of porcelain was related to the development of yue ware or celadon, high-fired stoneware that appeared in China in the Western Zhou Dynasty (1122 BCE - 256 BCE). Dragon kilns, long brick enclosures with fires built at the bottom that snaked up hillsides and glowed like dragons at night as they fired yue ware, have been excavated in numerous locations in China. By 600, the yue ware trade was large and sophisticated, and white porcelain appeared, replacing bronze and lacquer utensils for daily use. Sui Dynasty (581 - 618) potters achieved harder white porcelain with a cleaner glaze than yue ware. Chinese records during the subsequent Tang Dynasty describe jade- and ice-like yue ware so resonant that it could be made into bells. Government kilns brought together the best craftsmen and raw materials. Yue ware was prized because it was like jade, and white porcelain Xing ware was described in Chinese records as “silver-like” and snow-like.”
10th century yue ware. Metropolitan Museum of Art.
Some white porcelain was gaudily decorated with tri-color (sancai) glazes believed to have imitated popular Indian batiks which entered China over the Silk Road trade route. These vessels were achieved with metal oxide glazes, technology later developed further into the exquisite painted blue-and-white porcelain that became famous in Europe. Tang potters made elaborate figures depicting Tang Dynasty life, including detailed figurines of horses and traders on camels traveling the Silk Road to India. White porcelain was traded as far away as Iraq and Egypt.
A sancai horse. San Francisco Museum of Art.
Sancai dish in the shape of a flower. San Francisco Museum of Art.
Porcelain conveyed designs between East Asia and the Middle East for centuries. Porcelain got a major boost when Lu Yu (733-804) wrote his famous Cha Jing (The Classic of Tea) which set off a craze for tea drinking and the development of elaborate social tea-drinking rituals using tea vessels. Lu wrote that yue ware was the best bowl for presenting tea. During the Song Dynasty (960-1279), Chinese potters made a delicate pale blue type of porcelain called Qingbai, or bluish white. Qingbai turned the porcelain center of Jingdezhen in eastern China’s Jiangxi province into a major industrial complex with more than 300 kilns during the 12th and 13th centuries. International markets for Qingbai included Korea, Japan, Southeast Asia, the Middle East, and Egypt. Luanbai ware, which was eggshell white, succeeded Qingbai ware as a popular export.
Jingdezhen’s paramount position was threatened in the 13th century, when potters digging deeper for porcelain stone found that stone that was less weathered by natural elements caused their objects to warm easily or collapse during firing. Potters solved the problem by mixing kaolin with porcelain stone, a breakthrough that enabled them to make more intricate, larger objects.
Items made for the Islamic market were among the first to make their way to Europe. The Chinese called both stoneware and porcelain, which are produced by similar technology, ci. The term porcelain originated in Italy to describe imported Chinese wares with a shiny, white, shell-like surface similar to that of piglet-shaped cowrie shells. Europeans had produced stoneware for centuries, but it was bulky and oversized next to the translucent Chinese porcelain, considered magical because the Chinese held the secret of its manufacture. The earliest documented example of Chinese porcelain in Europe is the qingbai Fonthill vase, which dates from about 1300. Ladislas the Great, King of Hungary, gave it to Charles II of Durazzo on his ascent to the throne of Naples. The vase arrived in Europe at about the same time as Marco Polo returned from the East to describe the azure Qingbai bowls and give an inaccurate description of their manufacture.
In the first half of the 14th century, the Mongols ruled China, incorporating it into their vast empire that stretched westward to the Black Sea. Influential foreigners traded and lived in China, especially Arabs and Persians. Foreigners outnumbered Chinese in the Imperial Bureau of Manufactures, the government agency that had jurisdiction over porcelain production. Middle Easterners preferred brightly painted porcelains to the delicate understated monochrome porcelain favored by China’s elite. The Middle East was a ready market for painted blue-and-white porcelains which used Persian cobalt for the blue. The Mongol rulers were eager to increase their revenues from exports such as ceramics. The blue-and-white porcelain trade expanded rapidly. The porcelain was formed into large plates for communal eating common in the Middle East and painted in styles reminiscent of Persian miniatures and textiles.
The design on this Yuan dynasty plate shows the influence of Central Asian textile designs. Metropolitan Museumof Art.
The shape of this Ming flask and the design on its face indicate Islamic influences from West Asia. Metropolitan Museum of Art.
After the decline of Mongol rule in China and the rise of the Ming Dynasty (1368-1644), trade was restricted and porcelain exports dropped along with imports of Persian cobalt. Blue-and-white porcelain increasingly reflected Chinese aesthetics, with imperial symbols such as the dragon and phoenix and floral motifs.
Ming jar with a lotus pattern. San Francisco Museum of Art.
Jingdezhen was ideally situated to take advantage of a reviving demand for porcelain as the Ming stabilized. The city’s location on the Chang River provided convenient water transportation to Lake Boyang, which connected to a network of waterways, including the Yangzi River. The waterways linked Jingdezhen with the Grand Canal going north and rivers going south to the southern port of Guangzhou (Canton) and other major seaports and cities. Jingdezhen had an abundance of porcelain stone and kaolin left by volcanic eruptions, along with pine for fuel.
The Chinese created the first large-scale factories in which ceramics were mass-produced using specialized workers. In the 16th century in the imperial kilns, more than 500 master potters and workers were divided among 21-23 departments. A potter throwing small bowls was expected to produce 100 per day, and one making large vessels was to produce ten. The red fire of kilns glowed and filled the air with rising smoke.
The industry was linked with a sophisticated trade network that had developed concurrently with it over centuries. Korean potters had copied Chinese ceramics since the third century and became masters of celadon and porcelain whose wares were sought after in China. Japan-China trade flourished in the Tang Dynasty (618-960) when the Japanese court emulated the Tang and sent embassies that carried Chinese ceramics to Japan in return for Japanese gold, sulfur, wood, and other products. Chinese made some porcelain objects, such as sutra containers, only for the Japanese market. Chinese traders sailed on two main routes -- the East Seas route to Korea and Japan, and the longer, more complex South Seas route that included the lands of Southeast Asia and beyond. Since the late 2nd century BC, China had been linked in the east with Iran and Italy in the Mediterranean over more than 7000 kilometers of the Silk Road. Goods were exchanged at trading centers along the way, many of which became centers of culture and art.
The sea Silk Road route to the regions west of China expanded greatly when the decline of the Tang Dynasty rendered China unable to safeguard the land route. Navigators and shipbuilders improved their skills and ships until maritime trade became more economical than land travel. Chinese goods flowed to India, the Persian Gulf, the Red Sea, and Egypt by sea. The Office of Maritime Trade in the 10th century had jurisdiction over trade with 68 countries and regions. In the eleventh century, the Chinese dramatically increased direct maritime trade, traveling to Vietnam, Cambodia, Thailand, Malaysia, Indonesia, Sri Lanka, India, Yemen, Syria, Egypt and south to Somalia in junks guided by compasses. Chinese junks stopped on the east coasts of India and Sri Lanka or along the Strait of Malacca to trade, then at southern ports such as Brunai and the Philippines on their way home. The Chinese exchanged their goods with Arabs and Indians for luxuries and Indian cotton cloth, then resold those along with Chinese goods in Southeast Asia for spices. Enormous amounts of Chinese ceramics have been found at coastal sites in southeast Asia. Some were objects made exclusively for the Southeast Asian market. From India to East Africa, archaeologists have found more than 70 ancient sites that imported ceramics from China. Other 10th century shards have been found in Sri Lanka and Europe.
By 1349, China traded with 99 countries, of which 44 imported Chinese ceramics. Ceramics were too fragile and heavy to ship in large quantities by land, but maritime transport enabled their export to expand greatly. Porcelain became a measure of status and wealth in importing countries. The Chinese used ceramics income to stem their outflow of copper cash, which had become an international hard currency. In Guangzhou and the Hanoi area in Vietnam, Chinese porcelain was traded to Middle Eastern merchants, intermediaries between China and countries further west, for Indian cotton cloth, Roman glass and spices of India and Southeast Asia. Shards of Tang white porcelain have been unearthed in Iraq and Iran.
Islamic potters tried to imitate Chinese wares using tin oxide glazes to achieve a white surface over brown pottery. In Egypt, potters copied Chinese blue and white wares in pottery as soon as they arrived. Ottoman blue-and-white pottery had Chinese-influenced designs, probably taken from war booty looted by the Turks in Iran, Syria, and Egypt during the Ottoman conquests of the 1520s. Vietnamese blue-and-white porcelain competed with and supplemented Chinese porcelain. Thailand tried to imitate Chinese porcelain, creating its own distinctive wares. The earliest Korean blue-and-white wares were modeled on Chinese Ming examples and made with Middle Eastern cobalt imported by Chinese middlemen to Korea. The demand for Chinese blue-and-white wares spurred Japan’s production.
A 15th century Vietnamese plate. Metropolitan Museum of Art.
Under the Ming dynasty, the government prohibited private trade and withdrew from Asian maritime routes in 1523, just as the Portuguese arrived in Asia. Among the goods that Vasco da Gama had picked up in India in 1498 after sailing around the cape were Chinese porcelains which he took back to the Portuguese king. The Portuguese were banned from trade with China, but still traded with Chinese junks carrying goods including porcelain to the Portuguese-controlled port of Malacca. In 1557, the Chinese allowed the Portuguese to establish a trading post at Macao. Initially, porcelain was incidental to Portugal’s Asia trade - a convenient way to protect teas and silks against water damage. However, Portuguese ship crews purchased large amounts of china ware for their own use. The Portuguese primarily traded porcelain in Asia, not seeing its potential as a trade good in Europe. Portuguese ships sailed around the Cape, across the Indian Ocean, and up to Macao or north to the west coast of India and on to Macao through the straits of Malacca. From Macao, they went up the Pearl River and anchored at Whampoa in China. Their cargo was transferred to junks and ferried to foreign factories in Guangzhou (Canton). After trading for Chinese goods, they sailed to various ports in Asia where they sold most of the porcelain from Guangzhou and then headed back to Europe.
In the 1560s, the Spanish established their east-west trade between the Philippines, where they picked up Chinese porcelains, silks, and Asian spices; the Americas, where they traded for silver; and Europe, where they sold all of these goods. Manila became a Spanish colony in 1571, and the Philippines became a major commercial intermediary between China and the New World. So many Chinese merchants set up shop in Manila that the Spanish periodically massacred them to eliminate competition, sparking Chinese hostility that contributed to highly restrictive Chinese trade policies toward foreigners in China. Spain had an abundant supply of silver from the New World, which China wanted as payment for its goods and upon which it became dependent as silver had become its currency. More than a million taels of silver were exported per year from Manila to China; a third of all the silver mined in the Americas went to East Asia. The most widely accepted currency of exchange in the ports of East Asia were Mexican pieces of eight. Spanish galleons sailed from Manila to Acapulco, where cargoes were unloaded onto mule trains bound for Veracruz. From there, they were loaded onto Spanish ships headed for Seville, Spain. However, most trans-Pacific shipments of Chinese porcelain were sold in the New World. Mexico City became one of the richest cities in the world, as the products of Europe, Asia, and the New World poured into it. Mexican art and culture were heavily influenced by the designs of Chinese porcelain. A half-century of galleon trade brought millions of pieces of Chinese porcelain to the New World. For the Chinese, this was a fortuitous expansion of trade with the Philippines which they had been conducting since 500 BC. The volume of ceramic trade to Mexico was the greatest in the late 16th century, according to archaeological evidence in Mexico. After this, Chinese ceramics imports declined with silver depletion at the Zacateca mines in Mexico, restrictions on exports and changes in the Chinese exchange rate for silver.
Non-Chinese forms were copied in Chinese porcelain for Mexican tastes, including the alberello which can be traced to 12th century Persia; mancerinas, or cup holders; soperas or soap tureens in the shape of a cock or duck.
Some Chinese porcelains had a wild ride on the way to America. In the spring of 1579, Francis Drake raided Spanish galleons off the west coast of South and Central America and then replenished his supplies at Drake’s Bay, California. He abandoned or traded his cargo of Jingdezhen porcelains there. In 1595, the Spanish galleon San Agustin anchored at an inlet of Drake’s Bay. High winds drove the ship up on the coast, and it broke in pieces. Ceramic specimens found at the site are from Fujian, China. Ceramics found at Drake’s Bay are the earliest archaeologically datable examples of Chinese porcelain transported across the Pacific in Manila galleons. Other porcelains were victims of Dutch piracy of Spanish ships. The San Diego sank in an altercation with Dutch warships on Dec. 14, 1600 with more than 500 blue-and-while porcelains aboard. The Nuestra Senora de las Concepcion sank off the Mariana Islands near Saipan with Jingdezhen porcelains aboard. Pirates and hurricanes sank Spanish galleons sailing from Veracruz to Spain. Dutch shipwrecks also have been found. In cases where the dates of shipwrecks were known, recovery of the porcelains aboard have been important in the dating of porcelains found elsewhere.
Archaeologists have uncovered Chinese porcelains in the Zocalo area of Mexico City from Templo Mayor, the National Palace, the Animas Chapel of the Metropolitan Cathedral, and on nearby streets. Archaeologists have dated Chinese ceramics from a series of floods in the Zocalo area in Mexico City from 1629 to 1638. This has helped to date ceramics elsewhere.
Chinese plates with a deer design have been found in shipwreck cargos in the Middle East and at Drake’s Bay. Chinese ceramics dating from 1610 to 1680 have been found at the Palace of the Governors in Santa Fe, New Mexico, at the northern end of the El Camino Real where Spanish colonies were established by 1595. Chinese porcelains have been found at other sites in New Mexico that are similar to fragments in the Princessehoff Museum in the Netherlands and the Topkapi Saray Museum in Istanbul, Turkey.
Puebla, Mexico, had been an important ceramic center back into Aztec times, and it continued production in Spanish times, producing Majolica wares similar to those made in Andalusia and Seville, Spain. The lead-glazed pottery with a tin oxide additive had an opaque white surface on which Mexican blue cobalt oxide was applied. Puebla potters, who were midway on the trade route between Acapulco and Veracruz, imitated Chinese porcelains by developing finer-grained pottery and lustrous white glazes. A guild regulation issued in 1653 in Puebla said that “the coloring should be in imitation of the Chinese ware, very blue, finished in the same style and with relief work in blue.…” This gave rise to Talavera poblana, a style that persists today, and reflects Chinese influence in shapes, compositional formulas and design motifs. Chinese pagodas, phoenixes, and other symbols were incorporated into Hispano-Mooresque designs as well as shapes such as the pocillo, a cocoa cup which imitates the porcelain Chinese cup. On Puebla designs, the phoenixes were quetzal birds.
The Portuguese also shipped Chinese ceramics straight to Europe around the Cape. The ceiling of the porcelain room of the Santos Palace, Lisbon, is embedded with more than 260 late Ming porcelain dishes dating from the mid sixteenth century to 1613.
The Dutch supplanted the Portuguese in the Asian trade in 1594. In 1600, Britain founded its first East India Company. The Dutch formed the Dutch East India Company in 1602, and then captured a Portuguese ship, the Sao Tiago. The Dutch auctioned its contents, including blue-and-white porcelain, in Holland. Two years later, the Dutch captured another Portuguese ship, the Santa Catarina, with a cargo of about 100,000 pieces of blue and white porcelain and auctioned it. Among the buyers were James I of England and Henry IV of France. The ships were called carracks, or kraacks in Dutch. Hence, Chinese porcelain came to be called kraak porcelain in Europe. The buyers included the kings of England and France, and the auctions touched off a European mania for Chinese porcelain.
The Dutch imported more than three million pieces of porcelain into Europe between 1604 and 1657. The Chinese porcelain sold in Europe initially had Hispano-Mooresque and Italian border designs with Chinese symbols at the centers. The Dutch quickly realized that the best way to sell Chinese porcelain in Europe was to adapt them to European taste and table customs. As early as 1635, the Dutch provided the Chinese with painted wooden models of European silver and pewter shapes to copy. Later, they gave the Chinese ceramic and glass models and prints and drawings to copy. The Dutch also hired their own artists to make designs for porcelain.
The design of this Chinese-made plate was created by Dutch artist Cornelius Fronk. It was popular and was copied by not only the Chinese, but Japanese potters. Metropolitan Museum of Art.
In the 16th century, as porcelain and silk were traded internationally, Chinese cities and towns boomed. Around 1620, as the Ming dynasty declined, commercial kilns explored new styles in the absence of imperial constraints. Japanese potters also stepped in to meet the booming demand. The Jingdezhen kilns were destroyed in the turbulent transition from the Ming to the Qing dynasty but rebuilt in 1677. The Dutch also imported all-white porcelain wares made in Dehua in Fujian province to Europe, sometimes having them painted in Europe. Dutch special orders resulted in a proliferation of new designs, many of which combined Dutch and Chinese elements. However, the European trade at its height in the 17th and early 18th centuries was still of minor importance to China in comparison with Chinese porcelain trade in Asia.
The Dutch porcelain trade got a boost with the introduction of three new beverages throughout Europe during the early 17th century – tea, coffee, and chocolate. The Spanish court controlled the importation and consumption of chocolate in the 1500s and 1600s. The first commercial shipment of tea from China arrived in Amsterdam in a Dutch East India Company ship in 1610. Coffee, native to Ethiopia, arrived in Europe in the early 17th century via Middle Eastern trade routes. By the 18th century, Europeans were consuming them daily. European earthenware and metal vessels used for ale and wine were unsuitable for these expensive beverages, which were consumed in small amounts. Porcelain was ideal.
The French arrived in Canton in 1698, and the English the following year, ending Dutch dominance in the China trade. From 1730 until the end of the 18th century, England dominated trade with China, sharing it sometimes with France, Holland, Sweden and Denmark. More than 60 million pieces of porcelain were imported into Europe, with merchants in Guangzhou as middlemen in securing porcelain for Western ships. They kept stock porcelain patterns known to be popular in Guangzhou warehouses, along with undecorated wares that could be enameled and fired by local porcelain painters. The merchants also ordered custom sets from Jingdezhen. The process at first was difficult for Chinese potters, as the Europeans often gave them models that were difficult to produce and rejected them if they weren’t done to their liking. Such pieces would not sell on the Chinese market, so the potters were stuck with them.
As souvenirs for sailors, the Chinese decorated porcelain with Western ship designs and ports that the ships passed en route to Guangzhou, taking the designs from paintings or sketches. Porcelain painted with ships was mass-produced without the flags, which were added at the request of the buyer.
The thirteen hongs at Guangzhou shown in the bowl at the top of this page were groups of wood and brick buildings that foreign traders used as residences, offices, and warehouses. The hongs stretched along about a thousand feet of the Pearl River and the southwest edge of the city; each hong of two-to-three-story structures was connected by archways and courtyards. Between the front buildings and the river was Respondentia Walk, a promenade with flights of steps leading to boats that carried chaperoned pleasure parties by appointment. The only unsupervised outdoor recreation foreigners were allowed was on Respondential Walk, as the hong area was isolated from the rest of Guangzhou. Europeans were allowed no unofficial contacts with Chinese. The factories, generally leased by the month or for the five-month trading season, were regularly contracted year after year and came to be identified by nationality. The Danish factory was at the west end, followed by the Spanish, French, American, Austrian, Swedish, English, and Dutch. A fire in 1743 burned over 150 houses in the area. The images seen on Chinese trade punch bowls such as the one at the top of this article probably were rebuilt structures. The various types of hong bowls differ mainly in the flags on the hongs, by which the bowls can be dated.
The domestic Dutch Delftware tin-glazed pottery industry developed during this time, modeled on Ming porcelain designs. This development in the city of Delft coincided with beer brewers being forced out of business by excise taxes. Their abandoned brick breweries were ideal for potters, who were worried about fire. Some potteries kept the name of former brew houses. Delft porcelain design was a combination of Asian and European design, along with styles derived from the shawls of Kashmir, India.
This Delft pagoda in the British Museum has motifs that reflect both Asian and European influences.
By the beginning of the 18th century, Chinese porcelain was a luxury that filled special rooms in palaces from England to Russia. England’s Queen Mary II (1662-1667) started the craze with a large Chinese porcelain collection that covered shelves and walls from floor to ceiling in 11 porcelain rooms and encouraged similar rooms in the homes of European aristocrats. Porcelain was exchanged as gifts and accompanied princesses when they married other countries’ royalty. The Princess of Orange, Louise Henriette (1627-1667) took her collection when she married the Elector of Brandonburg-Prussia in 1646, and it eventually filled four rooms in the Orangenburg Palace near Berlin. The Italian Medici collection included 500 wares. Elaborate porcelain dinner services of hundreds of pieces were used on royal and aristocrat tables. After the mid-1660s, enthusiasm for porcelain sparked the decorating phenomenon known as Chinamania. Augustus, King of Poland, had more than 20,000 porcelains, including Chinese and Japanese ones. Porcelain was prized more highly in Europe than in China, where it was a common use item and lucrative export commodity but by this time not ranked as high as painting, calligraphy, seal carving and bamboo carving.
Among the most well known export porcelains were armorial services. These can be found as early as the 16th century, but the demand for them increased around 1700. Most 18th century European aristocratic families and wealthy merchants owned Chinese armorial dinner and/or tea services. From 1715 to 1805, the Chinese made 6,000 armorial tea or dinner services. Many families ordered several sets to commemorate special events such as rank promotion, marriage, or granting of arms. Wealthy merchants whose children married into the aristocracy ordered services with arms to which they were not otherwise entitled. A completely individualized service took two years from the order date to acquire. It was faster if the client had his arms added to a stock pattern in Guangzhou. Fashions in armorial styles changed and dishes can be dated from the styles.
Jesuit missionaries introduced Western taste in paintings, enamels, and prints to China’s imperial court in the 17th century, and Chinese elite purchased enameled objects from Europe. The Jesuits taught Chinese artists to enamel on copper in imitation of European enamels. Chinese applied the technique to porcelains. Rose pink was a feature of these objects, which are called famille rose and first appeared on export porcelain in about 1721. In 1728, the Chinese imperial glass factory at the Imperial Palace compound in Beijing succeeded in making its own type of enamels that differed from European ones. Famille rose enabled Chinese artisans to imitate reds, pink, and purples in Western paintings. The enamels were added to porcelain that had already been fired and were reheated enough to fuse the enamel. This breakthrough enabled an unprecedented joining of painting and porcelain in refined designs, brilliant colors, and exquisite details. The new techniques enabled shading in European-style painting on porcelain.
This Qing dynasty vase is a blend of cultural influences. Its shape is that of an ancient Chinese bronze vessel and the landscape painting is traditional Chinese, but some of the designs on it are European, possibly a result of Jesuit missionary influence.
The exuberantly colored famille rose style fit perfectly with the lavish use of color in the Qing court. It also contributed to the rococo style of Louis XV of France and was the mainstream of Chinese export ware to Europe in the 18th and 19th centuries, when porcelain was part of a European craze for Asian decor. Louis XV built a Chinese-inspired pleasure house covered in blue-and-white tin-glazed tiles in imitation of Chinese porcelain. Royal and aristocratic residences featured pagoda-inspired roofs and pavilions. Rooms were furnished with lacquer wall panels and furniture, and Asian-style textiles and wallpaper. In England, this reached a peak in the 1750s. Asian and Middle Eastern figures in flowing robes and elaborate headdresses that were a mixture of cultures characterized the style.
Exquisite colored Qing porcelains at the British Museum.
Jesuit missionaries had taught Chinese artists European perspective painting and engraving, which the artists applied to porcelain. East India companies brought European art forms such as enameled watch cases, coins, ceramics, and prints of popular European paintings with biblical and mythological scenes to Guangzhou to be copied. A black and white engraved look developed from Viennese factory prototypes. Canton became a clearing house for the exchange of European designs, eclipsing Chinese designs in the export trade for a time. By the end of the 18th century, Chinese-Western designs produced in Europe were sent to China to be copied. The Eight Immortals, sages, butterflies, frets, and panels of Chinese figures in a landscape or domestic scene were popular. Pictures of Chinese scholars in nature settings were particularly popular during the 18th century’s Age of Enlightenment, during which people sought to find philosophical answers in nature.
Design became a cultural free-for-all, similar to the experience of visiting a fabric store today and seeing fabrics from South Korea with stars and stripes and cloth from China with African designs. The designs were copied and exchanged by artists in other countries. The popular style known to Europeans as Fitzhugh is believed to have originally been called Fuzhou, after the southern Chinese city of Fuzhou. Some designs reflected the expansion of European empires. Europeans called the monochrome Yue ware celadon after Celadon, a character in the seventeenth-century French play Astree, who wore a gray-green costume that became the most fashionable color in Europe for a while. Yue ware became popular in Europe along with the color. The Chinese also exported shapes which had originally been executed in bronze and are now considered standard European décor.
The development of European tableware can be traced through Chinese export porcelain, which responded to changes in European fashion closely enough so that it offers guidelines for dating changes. European table services were elaborate. An American trader from Rhode Island who was in Guangzhou in 1797 wrote that a breakfast included a teapot, milk jug, sugar dish and stand, slop bowl, plate, and twelve cups and saucers. Additional pieces might have been a coffeepot, cake plate, butter boat, and stand. A tea or coffee service had forty-nine pieces. Dinner services averaged 171 pieces, including plates and platters ranging from six to 18 inches, some flat and some deep. There were soup, entrée, salad, and dessert plates, vegetable, pudding, and pie dishes, salad bowls, soup and pickle tureens, sauce and butter boats, fruit dishes with stands, salt containers, and punch bowls which were used before or after the evening meal.
The decline of the Chinese porcelain industry followed the trajectory of other native handicraft trades in areas influenced by European imperialism, especially the British trade. The Qing Dynasty court began to decline along with the imperial kilns that had pushed porcelain quality to perfection, while the European porcelain industry developed along with British global power.
Europeans had tried to master the secret of porcelain since the 16th century. Many Chinese claim that Jesuit missionary Francois Xavier d’Entrecolles stole the secrets of porcelain production and sent them to Europe but the secret actually was discovered in Europe before he sent his 1712 and 1722 letters to Europe describing porcelain production. Augustus the Strong (1670-1733), king of Poland, visited French King Louis XIV’s court, was enamoured with Louis’ Chinese porcelains, and commissioned treasures to rival Louis’. He spent so much money buying porcelain that the national finances were in chaos. He once traded King Frederick William I of Prussia 600 Saxon cavalrymen for 151 blue Chinese porcelain vases. To stem the hemorrhage of funds, Augustus desperately sought to discover the secrets of creating porcelain. He enlisted scientist Count Ehrenfried Walther von Tschirnhaus, who studied French and Dutch soft-paste porcelain experiments and learned how to construct a kiln. He experimented with using lenses and mirrors to concentrate solar energy in high temperatures, which gave him an understanding of the fusing of minerals. These experiments were crucial in attaining a kiln temperature high enough to fire true porcelain. Alchemist Johann Friedrich Bottger had fled to Saxony to avoid having to demonstrate bogus attempts to transmute lead into gold. Augustus imprisoned him in his castle. After he spent several years fruitlessly trying to create gold for Augustus, the king made him Tschirnhaus’ assistant. Bottgar researched clays and minerals and realized that pulverized rock, not clay, was the essential ingredient to add to fine white clay for porcelain. In 1708, the two men produced small white translucent porcelains using kaolin. At this juncture, Tschirnhaus died, and Bottgar succeeded in March 1709 in producing a white porcelain with a fine glaze. The next year, the first true porcelain factory in Europe was established at Meissen, where kaolin was available in large quantities. The potters in Meissen borrowed design elements from China and Chinese potters in turn copied Meissen designs. Porcelain factories were established in other areas. Royal marriages spread factories as the granddaughters of Augustus married other European royalty and established royal porcelain factories or encouraged their development in their new locations. Porcelain spread to Naples, Vincennes, France, Munich, and England. The mixed European-Asian design results were sometimes bizarre.
Meissen ware with an Asian theme painted in western perspective style, British Museum.
With the development of the British porcelain industry, British imports of Chinese porcelain began to decline in 1784. The British East India Company stopped importing Chinese porcelain by 1801. The newly formed United States, loathe to trade with the British, started trading New England ginseng, Hawaiian sandalwood, South Pacific sea slugs, and Pacific Northwest animal skins for porcelain. Chinese merchants and American traders formed close business relationships and Chinese merchants marketed in American newspapers. Great American fortunes were made in the China trade. Chinese porcelain fell in quality because of reduced demand from the Chinese court as its fortunes declined, while European porcelain quality improved. When the East India Company warehouse in Guangzhou burned in 1823, an order to replace a 1300-piece service originally manufactured in Guangzhou for the company was given to the Spode factory in England.
The population of Jingdezhen declined by 50 percent and the number of kilns dropped. In 1840, Britain defeated China in the first Opium War, forcing China open to foreign trade. Under the 1858 Treaty of Tianjin, foreign goods were exempted from local taxes while the Qing and local governments subjected Chinese-made porcelain to local taxes at every outpost along the way from production centers to markets. In Jiangxi province, porcelain from Jingdezhen was subject to a minimum 12 percent tax. Foreign porcelain became less expensive in China, and the Chinese industry tanked. A book written in the Guangxu Emperor’s reign (1875-1908), called More Information on China, recorded in Volume 180: “In former years Jingdezhen brought in five million taels of silver a year from its sale of porcelain vessels. Now the conditions are deteriorating and it gets less than half from its annual sales. Critics say the laws have not been properly drawn up and the taxes are too heavy!”
Americans developed their own porcelain industry and imported porcelain from Europe, complaining of poor quality and packing of Chinese porcelain. By 1800, the British imposed a 150 percent import duty on porcelain from China. The Jingdezhen kilns and the porcelain industry in Guangzhou were disrupted for a decade when the kilns were burned and the town’s population was killed or scattered during the Taiping Rebellion of 1854-1865.
Europeans still were trying to extract from the Chinese the complex chemical formulas for their superb glazes in the late 19th century. French consul Georges Francisque Fernand Scherzer spent three weeks at Jingdezhen in 1883 studying porcelain manufacture. Reluctant local officials and kiln managers were forced to go along with him because of extraordinary rights he had been given under the unequal treaties with European powers, but irate potters chucked potsherds at him until he could scarcely peep out of his closed sedan-chair. The Jingdezhen magistrate tried to show him around factories only at night, but Scherzer insisted that he would stay until he saw all operations in daylight. The magistrate gave in and put him in the care of the city’s troop commander so he could visit factories. At one factory, the manager categorically refused to give him the formula for the difficult copper red glaze that was one of China’s finest technical achievements, but Scherzer managed to obtain the information from employees. Scherzer wrote: “Today the Imperial buildings fall in ruins, the workrooms are badly kept, and the workmen, although recruited among the more skillful, receive a pay hardly more than that which is obtained in private factories.” The workmanship of the objects made in the imperial kilns was still high, he said. The French minister to Beijing had “demanded” that Scherzer be allowed to visit the city, so “the authorities could not do other than help me visit an active porcelain furnace.” Scherzer’s detailed report was accompanied by notes and sketches addressed to the Sevres plant in France and by porcelain samples. It enabled the French to “complete for the most part our knowledge relative to the manufacture of oriental porcelain.”
After the Sino-Japanese War of 1894, foreign firms were allowed to establish factories in China using China’s raw materials and labor to make and sell porcelain in China without paying import tariff. The factories mechanized production to further cut costs. Porcelain controlled by European factories flooded the Chinese market, with the profits exported. The indemnity imposed on China by the Treaty of Shimonoseki with the Japanese in 1895 was paid by foreign loans with Chinese customs revenue as security. This opened China’s customs to foreign control and resulted in restrictions on the export of Chinese porcelain. In the meantime, porcelain manufacturing grew and industrialized in other countries.
Jingdezhen’s porcelain production declined, its river transport channels silted up, and its workmanship deteriorated until just 110 private kilns operated in Jingdezhen, down from 1,000 in the 18th century. By 1905, most kilns only worked for a short time in the summer. Only about a sixth of Jingdezhen’s wares were exported. The demise of the industry was part of a larger decline in Chinese handicraft industries in the face of foreign competition. In 1903, the government allocated 100,000 taels of silver to establish the Jiangxi Porcelain Corporation at Jingdezhen. The factory was set up but the project failed because of embezzlement by Qing officials and wars. The corporation made a comeback during and immediately after World War I, when the European powers were occupied at home. The company produced exquisite wares that won medals nationally and internationally. However, foreign wares poured into China once again after the war and the company went bankrupt. A foreign traveler in 1923 described ruinous taxes to which porcelains and other goods were subjected by warlords who controlled various parts of China.
Jingdezhen has revived in recent decades with modernized, industrialized kilns that produce about a half million pieces of porcelain for export per day. Some porcelain replicas made in Jingdezhen today rival the quality of the best Ming and Qing porcelains. However, the city still faces stiff competition domestically and abroad. Jingdezhen suffered a recession in the 1990s when coastal porcelain factories with better equipment and technology opened. More than 60,000 ceramics technicians and workers left the city for coastal areas. Abandoned factories and workshops were turned into an art zone, galleries and an art community and the city opened a porcelain industrial park in 2015 to house porcelain manufacturing workshops for production and tourism. Master artists, some drawing on techniques their ancestors perfected over generations, now create coveted rare glazes that appeal to collectors. Pottery markets operate near workshops. China’s growing middle class has created a greater demand for Chinese porcelain. The city has almost 7,000 ceramic companies and workshops with some 150,000 people working in the porcelain industry, nearly a quarter of the urban population. Automated production lines from Germany offer mass production services for workshops which provide them with innovative designs. The technology uses 3D printing and other advanced technology.
The city also produces special ceramics for the aerospace and electronics industry. By 2017, the value of the city’s porcelain industry was 37 billion yuan, eight times that of ten years earlier. In an echo of the role of private industry across China, privately run workshops are driving the revitalization of the city and the surrounding areas.
After hundreds of years of extracting Jingdezhen’s clay, only about a million tons of it remain, about two percent of the area’s historic reserves. This poses new challenges as well.
Imperial-era Jingdezhen porcelain items fetch some of the highest prices in Chinese art, with a single Ming dynasty cup selling for $36 million in 2014 to a Shanghai businessman who paid for it with a credit card and then sipped tea from it.
Check out these related items
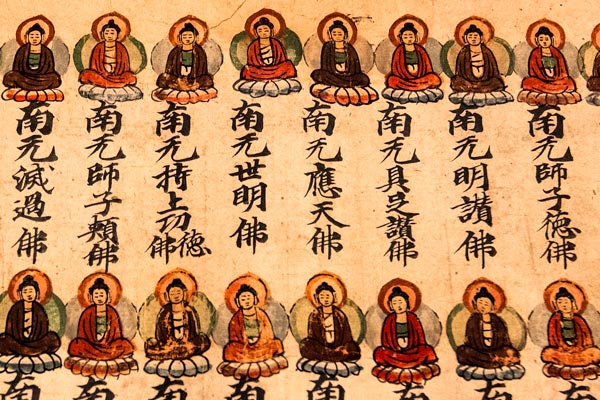
Ancient Silk Road Meets High Tech
The International Dunhuang Project digitizes old documents, caves and artifacts to enable global study of Central Asian history.
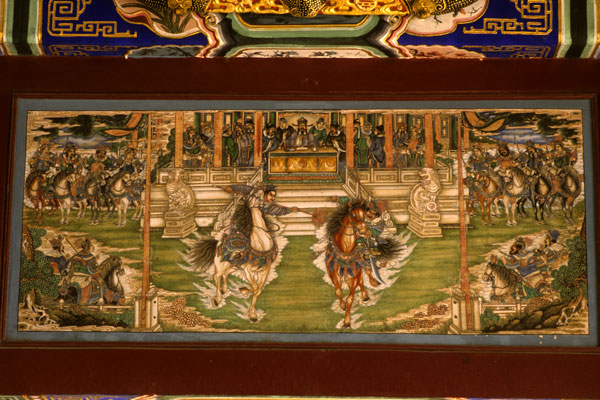
The Summer Palace
The Summer Palace, the most famous and heartbreaking of China's glorious imperial gardens, highlights dilemmas in the nation’s past.
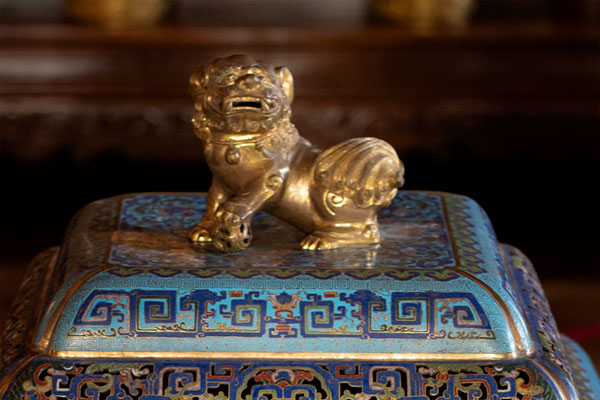
Treasure Room and Two Palaces
In the French palace at Fontainebleau is a treasure room of dazzling artifacts taken by the French army from a palace in Beijing.
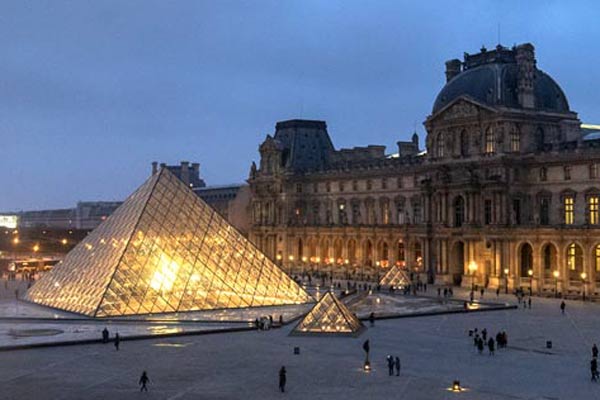
What is the Louvre?
The former palace, the world's largest museum, music video and fashion show venue, and global brand has never been more cool.
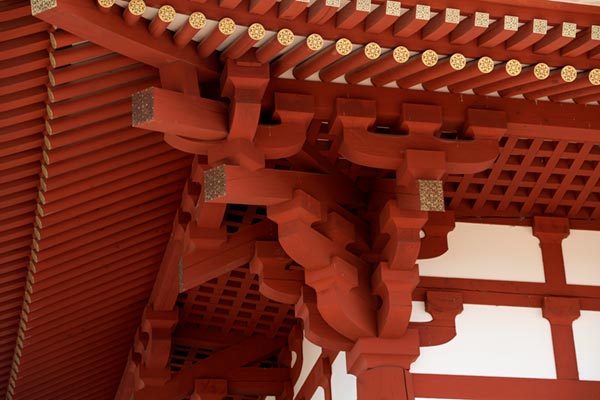
A Palace to Remember
Visible traces of the Heijō Palace, Japan's palace from which the emperor ruled in splendor, were gone, until the site was restored.
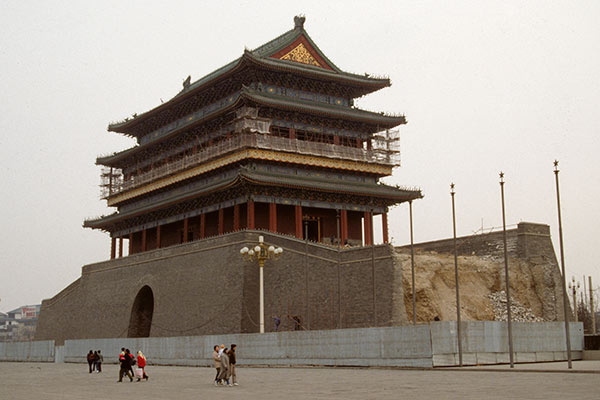
China’s Walled Cities
Only scattered remnants survive of the many walled cities that once defined the Chinese empire.